
I have it open right now and it’s using half the resources of cura.
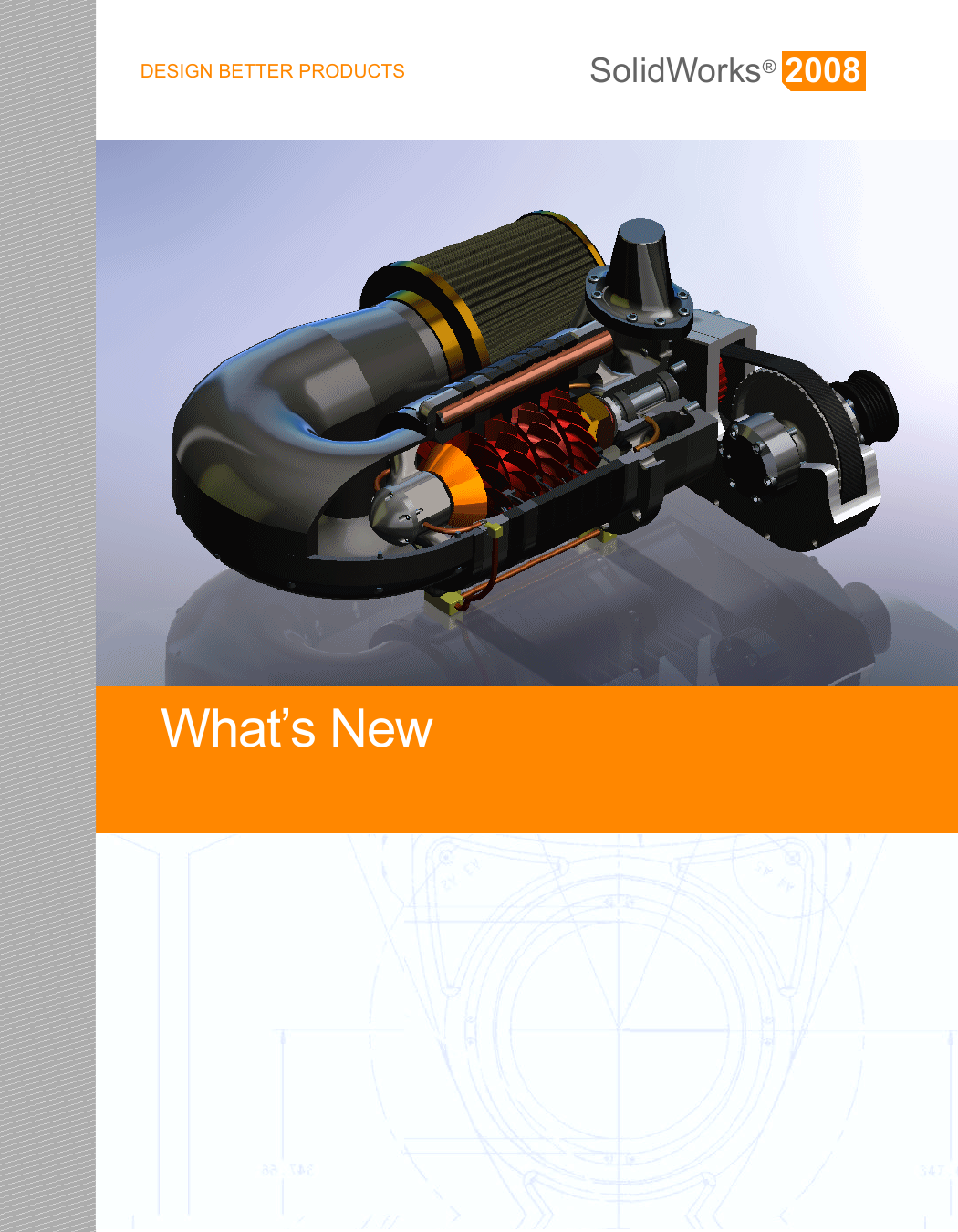
UI-wise, it’s super clean and fast, with a minimal of clutter. Here’s an impressive video on building involute gears with Solvespace: Being able to specify things with constraints makes life _so_ much easier, and once you get a handle on some of the more advanced gears doing semi-procedural designs by setting up geometric diagrams which are then used as constraints for individual parts which are then assembled into more complex structures becomes second nature. Not without its problems, and it requires a very specific workflow in order to be effective, but once the penny drops and you start thinking the right way it’s amazingly smooth.

I’ve been doing my modelling in Solvespace. I just got my first 3D printer (and have the box of random dead plastic prints to prove it). I really hope this is just temporary and we will get to create FOSS CAD which will achieve the same quality as Blender or Gimp did over the years… Also you don’t have to be afraid that you will lose your work if you bump into some bug, because the format is human readable and you can easily remove the problematic element from your model if it causes crash (which never happened to me).Īlso i think that since there is Fusion 360 for “free”, the development of FOSS CADs has kinda stalled. It’s quite different, but can be very effective and is the most stable from all of these.
#Solidworks 2010 bump bend part software
To be honest my most favourite FOSS CAD software is OpenSCAD. Like i wasnt able to add constraints which should be possible, etc… However once i tried to simulate such stuff using 3d models rather than plain lines, i started to bump into incomplete features. But i really liked the overall idea for simulating mechanical movement/linkages and i’ve used it to simulate linkages of hydraulic lifter that i’ve designed and made to be sure the leverages are about right. For example working with sheet metal, doing FEM simulations, etc… These things you can only do with FreeCAD. It obviously misses specialized workbenches/plugins which are available in FreeCAD. When i’ve messed with Solvespace for the first time i was quite impressed. I use it with 16GB, and have Inkscape, web browsers, and e-mail running at the same time, and it’s fine. However, whoever said you have to have 32GB of RAM to run FreeCAD is smoking something. SolveSpace can really start to chug if you add too many parts. I use both of them at home and at work if it’s something simple and quick, I use SolveSpace. Definitely two different mindsets, though. I get my share of issues when I do things I probably shouldn’t, like change something that other things are dependent on, and then have to work my way back through and fix everything that broke, but I still think it’s well worth the effort to learn. Some of the add-on modules are amazing – like the one for bending sheet metal. I also invested quite a bit of time watching tutorials and learning FreeCAD, and I’m generally very pleased with it. I just wish there was a way to go back and insert intermediate operations after the fact without the whole thing blowing up in your face half the time. I grew up with DOS apps, so the appearance didn’t really put me off.
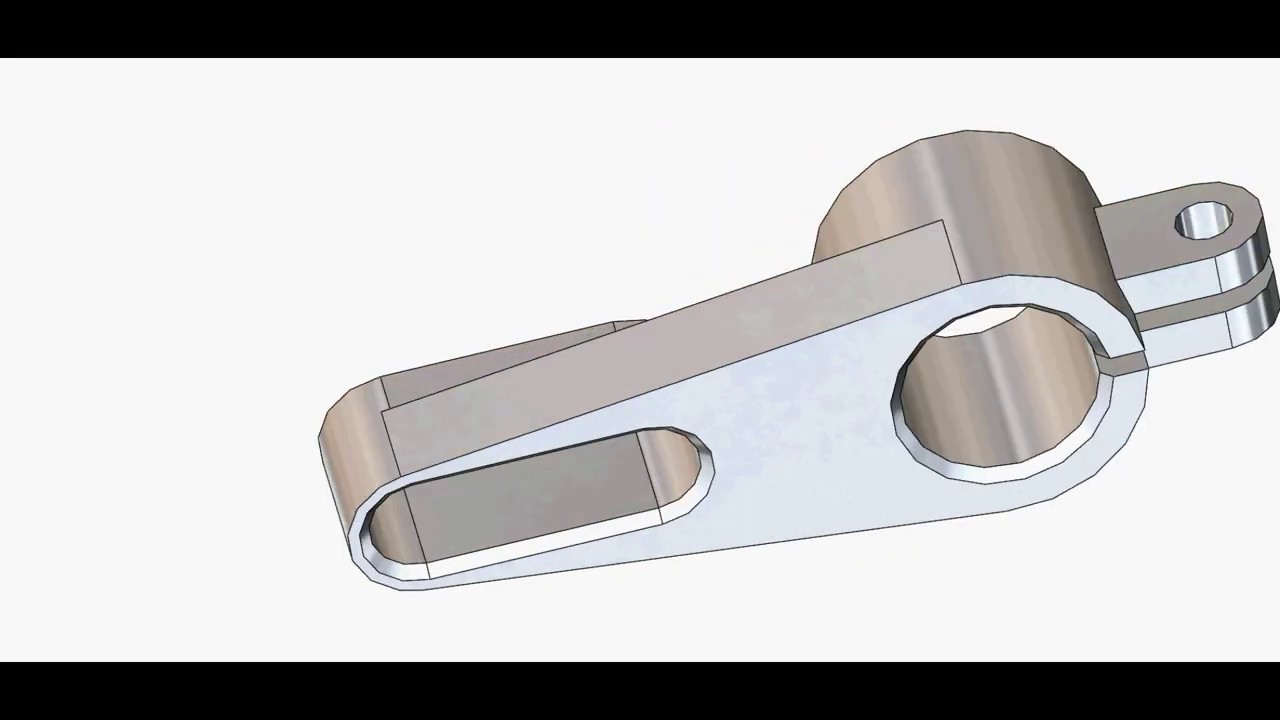
It’s extremely efficiently built (I mean – come on – it uses ONE single executable file!) and it’s pretty easy to learn. I started out with SolveSpace a couple of years ago, and I concur with your assessment. Posted in 3d Printer hacks Tagged 3d modeling, cad, freecad, solvespace Post navigation And we’ve talked a lot about FreeCAD, too. So, generally, we reach for FreeCAD but it is mostly because of habit. We haven’t used it as much, though, and FreeCAD integrates nicely with OpenSCAD which we use a lot, too. Our choice? We often use FreeCAD although we like how SolveSpace handles certain things. Being able to see the differences between the two tools might convince you to learn one or the other or maybe even switch. You probably don’t need this particular design, but watching over someone’s shoulder while they do a complex design can be very valuable. There are many tools that can do that, including FreeCAD and SolveSpace, two programs that uses to create a complex compressor blade and it really shows the differences and similarities between the two tools. For example, you can create a vertical line and constrain other lines to be parallel, perpendicular, or form a given angle with that line. Serious modern designs tend to use parametric modeling where you don’t necessarily set dimensions and positions of everything but instead constrain the design by describing the relationship between different elements. When you are ready to design real things, you’ll find simple CAD programs can be pretty limiting.
